QUALITY AND CONTROL
Since the inception, Quality has been the prime concern for the Keda Ceramic. All of our manufacturing plants have obtained ISO certification which confirms the quality of the products and services as well as the environmental and safety standards.
Every production is treated with the highest level of quality standards and taken utmost care with our latest machinery and personal monitoring. Each tile passes the individual supervision under the highly skilled eyes of the production team.
During the process of production, a dedicated set of people keep the records of the quality parameters. They submit the reports to the sales office which can be used to forward further or to store in the records. In case the products are not as per the set of quality parameters, then they report it to the production team and they work together to resolve it as soon as possible. As a result of this utmost focus and dedication towards the quality of products, Keda Ceramic has achieved the remarkable response from our customers around the world.
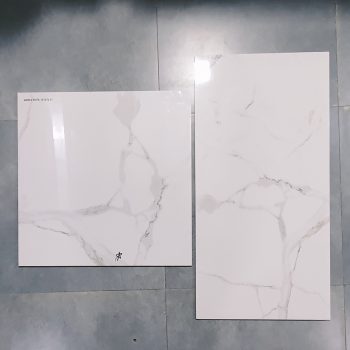
1. COLOR MATCHING
For every product in our collection, we maintain the master tile in the design office at the factory. Before the production starts, our design and quality team match the color and surface of each product by taking a sample tile. Once it is approved, the actual production starts. This process maintains the product color and surface consistency in every production.
2. SURFACE FLATNESS
When the product comes out of the kiln, it passes the polishing (if required) and rectification process. During this process, our quality team inspects the surface flatness report by flatness machines as well as by manual inspection. Surface flatness is one of the most important attributes of any tile and it is our priority to maintain that as per international standards.
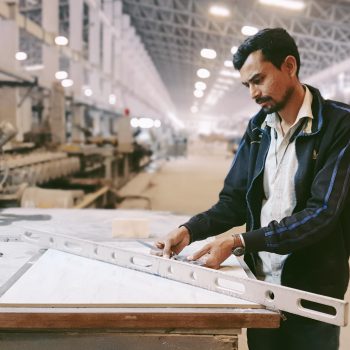
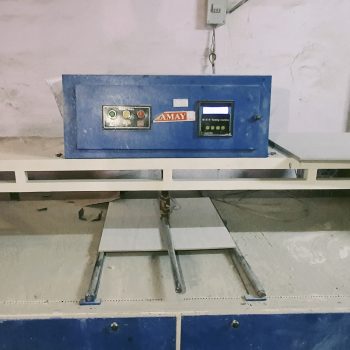
3.FLEXURAL STRENGTH (MOR)
We check the MOR twice during the process of tile production. First is in the laboratory, when we test the raw material and we make a micro tile. Second is during the production of actual tile and it is getting packed. We have a MOR test machine at each factory to check the parameter.
4. WATER ABSORPTION
We check the absorption report of the tile on the daily basis. For that, we heat the tile in the water and then cool it down. After that we check the water absorption by the WA machine. Our porcelain tile maintain WA under 0.05% and ceramic tile maintain WA between.
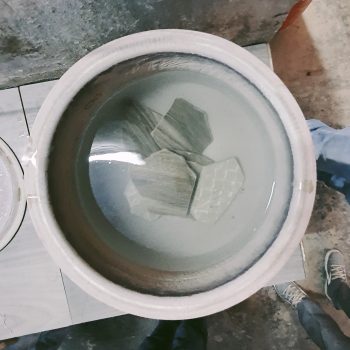

5. SHADE VARIATION
Before packing the tile, the sorting team checks the shade of the tile. We maintain a batch number for each shade of the tile. Generally for the less quantity production of a particular design, we have one batch / shade of the tile per production. For highly sensitive colored tiles or for large quantities of the one design, we have to manually check each tile before packing. They give a name of multiple batches during the production of each product.
6. DEVIATION IN LENGTH & WIDTH
We have to check the dimensions after the rectification of tile. The parameter should be as per ISO regulation. We check the length from the sides, diagonal length as well as the thickness of the tile for each batch of the production.
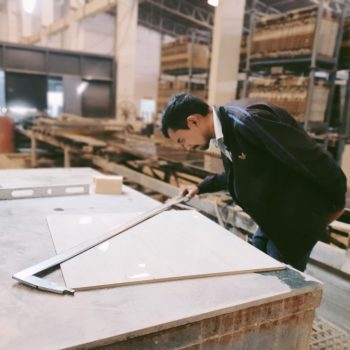
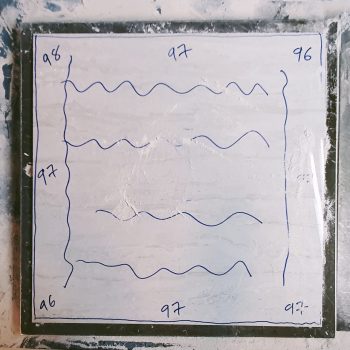
7. MARKER TEST
We choose the tiles randomly from any particular batch and we do the marker test on them. For that, we have run a marker / ink on the edges as well as central parts of the tile and then we clear them with the powder. The tile passes the marker test if the ink is removed with ease.
8. GLOSSINESS
This test is particular for the polished tile. For the polished tiles, the glossiness factor is very important. We check this on a regular basis during the production and we maintain the glossiness above 95 %.
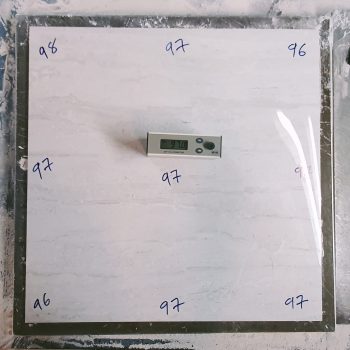
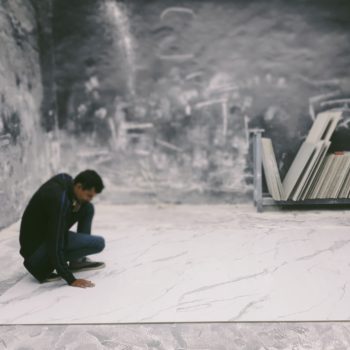
9. OTHER SURFACE RELATED PROBLEMS
After the tile passes above parameters, we lay a few tiles on the floor and check for any other surface related problems. This includes checking for the pin holes, polishing patches, kiln dust, etc. This process has to be done manually by an expert in quality inspection of the tile.
10. LOADING SUPERVISION
During Loading Supervision, an Ceramic Exporter representative will closely monitor the loading process, verify product quantity, and ensure proper handling of the cargo and its quality. Upon completion, the containers will be sealed with KEDA CERAMIC tape as proof of compliance. This service significantly reduces the risk associated with importing cargo.
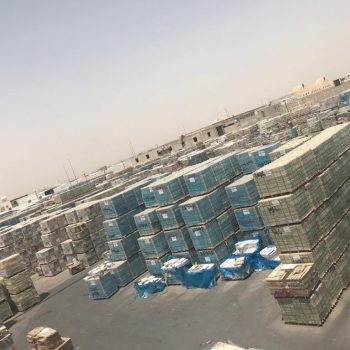
MEMBERSHIP & AFFILIATION
Do you have any Question?
Ready to Help you with Whatever you Need.